A horizontal CNC lathe is a computer-controlled machining tool used primarily for turning operations, where the spindle is oriented horizontally. It is widely used in automotive, aerospace, and metalworking industries for producing precise cylindrical components. In this guide, we’ll explore what it is, how it works, its benefits, and whether it’s the right choice for you.
What is a Horizontal CNC Lathe?
A Horizontal CNC Lathe is a precision machining tool used to rotate a workpiece on its axis to perform various operations such as cutting, sanding, knurling, drilling, or deformation. These lathes are controlled by computer numerical control (CNC) systems, ensuring high accuracy and repeatability.
Key Features of Horizontal CNC Lathes:
- Horizontal Orientation: The spindle is horizontally aligned, making it ideal for turning cylindrical parts.
- CNC Control: Utilizes computer software to automate and control machining processes.
- ความอเนกประสงค์: Capable of handling various materials like metals, plastics, and composites.
การใช้งาน:
- Automotive: Manufacturing engine components.
- Aerospace: Producing high-precision parts.
- General Manufacturing: Creating custom parts for various industries.
Horizontal CNC Lathes are essential for industries requiring precise and efficient machining of cylindrical components.
What Are the Key Components and How Does It Work?
The key components include the main elements that contribute to the functionality and efficiency of a system or process. It works by integrating these components to achieve a specific goal or perform a particular task seamlessly.
Key Components:
- Input: Data or stimuli required to initiate the process.
- Processing Unit: The core mechanism where input data is transformed.
- Output: The end result or product after processing.
- Feedback Loop: System for monitoring and adjustments.
How It Works:
- Input Phase: Collect necessary data or resources.
- Processing Phase: Utilize algorithms or mechanisms to transform input.
- Output Phase: Generate results or final product.
- Feedback Phase: Monitor performance and make necessary adjustments.
This streamlined approach ensures efficiency and accuracy, enabling smooth operation and continuous improvement.
Horizontal vs Vertical CNC Lathe
A horizontal CNC lathe positions the spindle parallel to the ground, optimizing for bar work and long shafts. Conversely, a vertical CNC lathe holds the spindle perpendicular, excelling at large, heavy workpieces and offering better chip evacuation due to gravity.
Key Differences:
- Spindle Orientation:
- Horizontal: Parallel to the ground.
- Vertical: Perpendicular to the ground.
- Workpiece Types:
- Horizontal: Ideal for long, slender parts.
- Vertical: Suited for large, heavy components.
- Chip Removal:
- Horizontal: May require additional mechanisms.
- Vertical: Gravity aids in efficient chip evacuation.
- Footprint and Space:
- Horizontal: Generally requires more floor space.
- Vertical: More compact, freeing up floor space.
การใช้งาน:
- Horizontal CNC Lathe: Automotive parts, cylindrical components.
- Vertical CNC Lathe: Aerospace parts, large molds.
Considerations:
- Cost Efficiency: Match the lathe type to the job requirements to optimize both cost and productivity.
- Precision Needs: Evaluate based on the complexity and tolerance requirements of the parts being produced.
In conclusion, choose a horizontal CNC lathe for long, bar-like workpieces and a vertical CNC lathe for heavy, bulky items, considering space, efficiency, and specific application needs.
Advantages of Horizontal CNC Lathes
Horizontal CNC lathes offer several advantages, including high precision, versatility, and efficiency in manufacturing complex parts. These machines are designed for easy setup and operation, reducing downtime and increasing productivity.
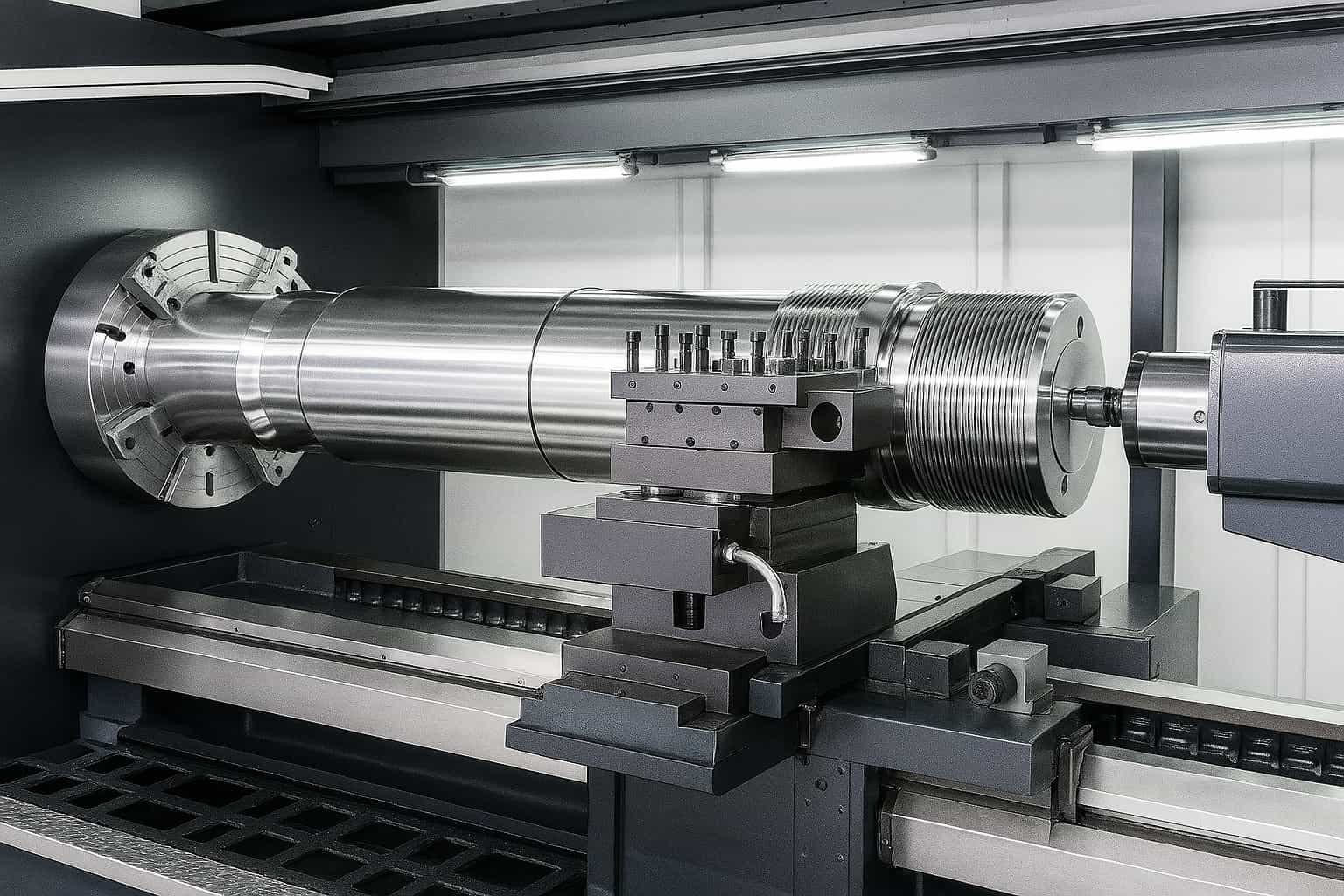
Key Benefits:
- Precision and Accuracy:
- Horizontal CNC lathes provide consistent, high-quality results, essential for industries requiring exact specifications.
- ความอเนกประสงค์:
- These machines can handle a wide range of materials and part sizes, making them suitable for various applications.
- Efficiency:
- With automated functions, horizontal CNC lathes minimize manual intervention, thus speeding up production processes.
- Ease of Use:
- User-friendly interfaces and programmable controls simplify machine operation and reduce the learning curve for operators.
- Cost-Effectiveness:
- By improving production speed and reducing waste, these lathes lower operational costs over time.
Horizontal CNC lathes are thus a valuable asset in modern manufacturing, offering a blend of precision, flexibility, and efficiency.
What Are Common Applications of Horizontal CNC Lathes?
Horizontal CNC lathes are widely used for their precision and versatility in various industries. They are primarily employed for turning operations on metal and plastic materials, creating components such as shafts, bolts, and gears with high accuracy.
Key Applications:
- Automotive Industry: Manufacturing engine components, drive shafts, and brake discs.
- Aerospace Sector: Producing turbine blades, landing gear parts, and structural components.
- Medical Field: Crafting surgical instruments, implants, and prosthetic parts.
- General Manufacturing: Creating custom machine parts and tools, threaded components, and bushings.
Benefits:
- High Precision: Ensures tight tolerances and smooth finishes.
- Automation: Reduces manual labor and increases production efficiency.
- Flexibility: Suitable for both small batches and mass production.
How to Choose the Right CNC Lathe
Choosing the right CNC lathe involves understanding your specific machining needs, evaluating machine specifications, and considering key factors such as size, power, and control systems.
- Assess Your Machining Needs: Determine the material type, part complexity, and production volume. This helps in selecting a lathe with appropriate capabilities.
- Evaluate Machine Specifications:
- Size and Capacity: Ensure the lathe can handle your workpiece dimensions.
- Power and Speed: Match the spindle power and RPM to your material and production speed requirements.
- Control Systems: Choose a user-friendly control system, compatible with your existing software and equipped with advanced features like real-time monitoring.
- Durability and Precision: Opt for machines with robust construction and high precision to ensure long-term reliability and accuracy.
- Support and Maintenance: Consider the availability of technical support and ease of maintenance.
By focusing on these criteria, you can select a CNC lathe that meets your operational demands efficiently.